What You Need to Know Regarding the 2019 USP General Chapter <797> and <800> Updates
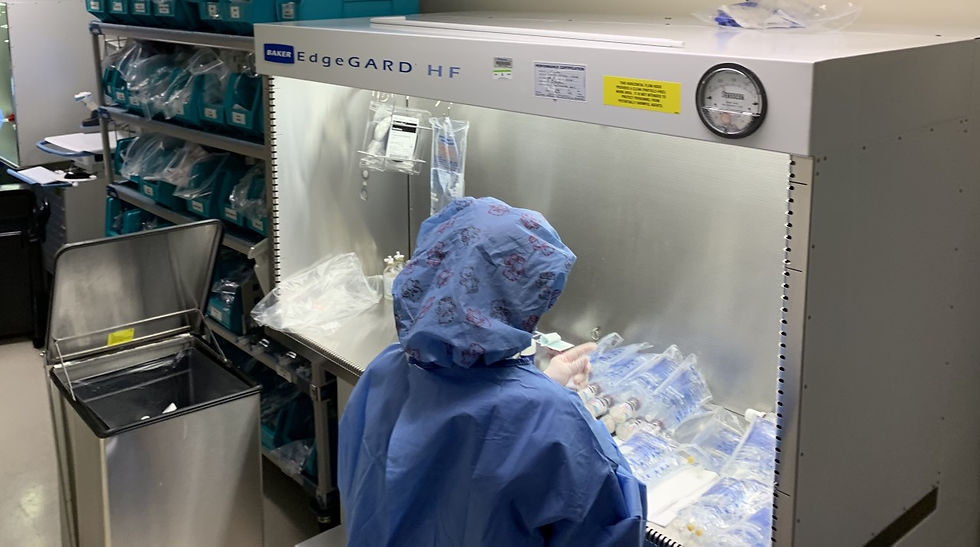
With the recent December 1st deadline to meet updated USP standards for compounding pharmacies, many facilities are in the process of making important updates that facilitate the safe handling of drugs. There have been some frequently asked questions during this time of transition, as well as common misunderstandings due to some of the wording in the General Chapters. Since implementation date and storage requirements have been two of the largest topics for discussion, it is worth delving into these matters deeper.
2019 revisions of USP General Chapters <795>, <797>, <800>, and <825> were all set to become official on December 1, 2019. However, as three of the updated chapters are now under a pending appeal, only the 2019 revision of USP General Chapter <800> became official on that date. Although it is for information purposes only and will not be compendially applicable while the other chapters’ appeals pend resolution, it is highly encouraged to start making necessary USP <800> upgrades during the appeals process. In short, facilities will have slightly more leeway in their timelines to make facility updates to be in compliance with USP <800> requirements, but the timeline is unknown and therefore should not be used as reason to delay needed upgrades.

Another question that surfaces frequently regards the storage requirements that are discussed in General Chapter <800> Hazardous Drugs – Handling in Healthcare Settings. Since the text calls for a “designated area” for hazardous drugs and describes it as “an externally ventilated, negative-pressure room with at least 12 air changes per hour,” there has been a common interpretation that the room must be used for nothing other than storage. However, the text does not state this. Hazardous buffer rooms, both sterile and nonsterile, meet the requirements stated for storage areas, and therefore can serve as the designated area for hazardous drug storage; this being said, it is recommended to clearly delineate the portion of the room used for storage to prevent unnecessary traffic through the immediate compounding areas. Furthermore, although separate rooms are not required for HD storage if enough room is allocated within the HD buffer, there could be some benefits to separating the spaces.
If the designated storage area is within a sterile HD buffer room, then it must meet the requirements stated in General Chapter <797> Pharmaceutical Compounding – Sterile Preparations in addition to <800>. <797> requires a minimum of monthly cleaning and disinfecting of storage shelving within compounding areas, which could be a substantial amount of cleaning depending on how large the HD storage area is. However, <800> does not specify cleaning requirements for rooms dedicated for HD storage, and it also does not specify that the storage area must have an ISO Class rating. Therefore, not only can hazardous drugs be walked directly into the room without the need to maintain an ISO Class environment, but each facility can set its own cleaning schedule as appropriate in its Standard Operating Procedures. Furthermore, a pass-through chamber can be placed between the HD storage room and HD buffer room to facilitate the easy transfer of drugs between the two areas.

Although storage only touches the surface of changes that facilities will need to make, it is oftentimes the most difficult in terms of working within existing spaces. Understanding that an entirely different room is not a written requirement may help to promote other ways of satisfying the USP <800> text within existing space constraints. By paying careful attention to what USP states “should” be done versus what “must” be done, facilities can start prioritizing upgrades to meet compendial requirements before planning more invasive renovations to create ideal environments.
Comments